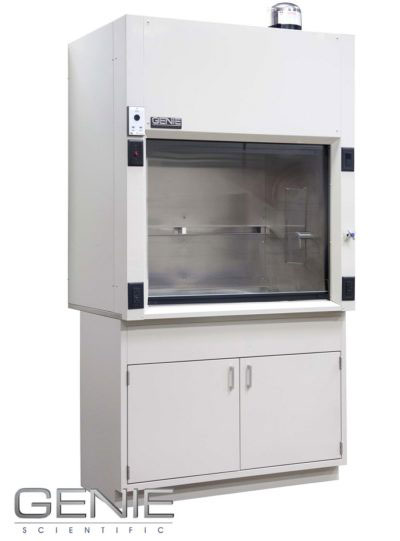
Fume hoods go through a certification process when they are manufactured. These processes are designed to ensure the hood will satisfy state, federal, and international certification guidelines, as well as those that meet or exceed current ISO9001 standards. In addition, the certification is part of the requirements to comply with standards and regulations prescribed by various agencies, including: • SEFA (Scientific Equipment and Furniture Association) • OSHA (Occupational Safety and Health Administration) • ASHRAE (American Society of Heating, Refrigeration, and Air Conditioning Engineers) • NEBB (National Environmental Balancing Bureau) • AIHA/ANSI (American Industrial Hygiene Association/American National Standards Institute)
There are specific test procedures used to evaluate the fume hood’s airflow velocity, airflow monitors, airflow gauges, cross-draft air flows, tracer gas containment, and so on. Long before these tests can be performed, the first step in certification is to calibrate the hood, airflow monitors, gauges, and motors.
The calibration has to be performed to verify these items are working correctly and the face velocity of the airflow is within acceptable parameters. Most agencies accept a minimum face velocity of 100 fpm (feet per minute) and a maximum of 120 fpm, and they tend to use 115 fpm as a standardized calibration since it is sufficient for a wide array of general usages.
After a fume hood has been initially certified by the manufacturer, laboratories, universities, healthcare facilities, and other organizations where the hoods are installed must ensure they have policies and practices in place to re-certify the hood on an annual basis, at the minimum. Some operations will re-certify their hoods bi-annually or quarterly, depending upon the amount of use and volume of chemicals and materials being used under the hood.
Anytime a hood is re-certified, the certification sticker on the hood should be updated. Any hood within your organization that either does not have a certification sticker, or has one that was last certified more than a year ago, should not be used until the hood can be tested and re-certified.
Re-certification testing checks the face airflow velocity using an acceptable measuring device, like an electronic digital anemometer, and verifies other devices and functions are working within prescribed and acceptable parameters.
Some organizations outfit their hoods with special monitors that constantly monitor face airflow values. These devices will sound an alarm and alert employees that the airflow has dropped below acceptable minimum levels. The use of monitoring devices is highly recommended, as it helps increase safety in work environments and reduces the risks associated with workplace accidents related to poor venting.
In between annual certifications, regular laboratory inspections should be conducted on all hoods. All monitors and other measurement devices should be checked to ensure they are working properly. In addition, the inspection should verify good housekeeping practices are being followed and practiced.
Anytime a hood is found to not be working correctly or fails testing guidelines, its use should be discontinued immediately until it can be fixed, repaired, and retested. For assistance in laboratory planning, installation, furniture, workbenches, hoods, and other products, call Genie Scientific at 800-545-8816.