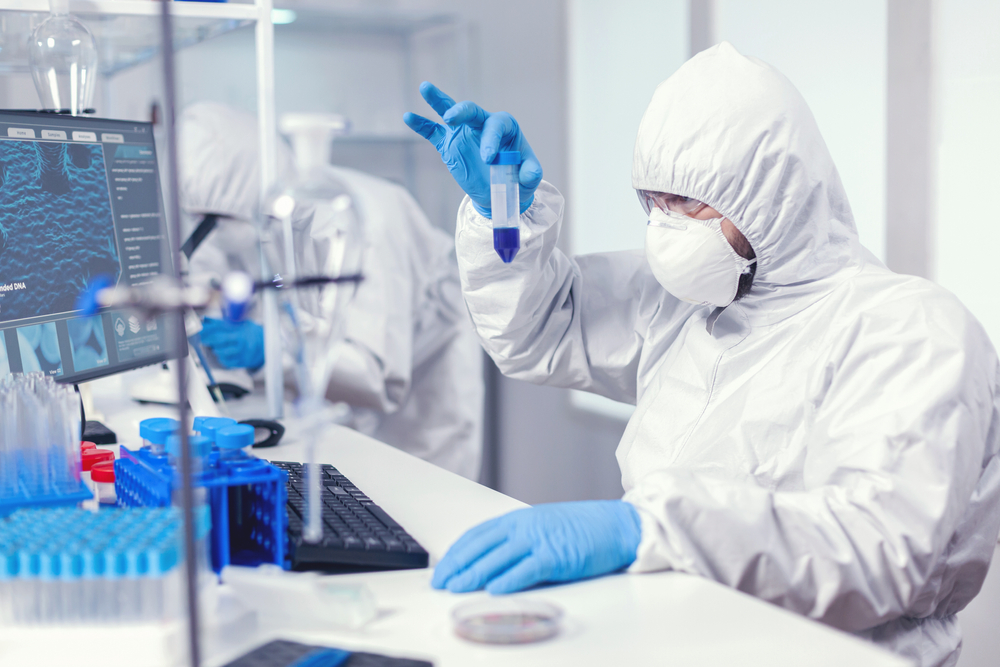
Precision is paramount in the world of scientific research and advanced manufacturing, and even the smallest contaminant can spell disaster. A clean room laboratory serves as the backbone of these high-tech environments, providing a controlled space where strict contamination protocols are upheld to protect both the integrity of the work and the safety of the outcomes.
Whether it’s a clinical laboratory, a pharmaceutical lab developing life-saving drugs or a semiconductor facility crafting the next generation of technology, maintaining a contaminant-free environment is non-negotiable. As the demand for more stringent clean room laboratory environments continues to grow, so too does the complexity of designing and maintaining these spaces.
This article delves into the essentials that make a clean room laboratory truly effective, exploring everything from the critical design features that prevent contamination to the best practices that keep these labs running at peak efficiency.
For laboratory designers and operators alike, understanding and implementing these essentials is key to ensuring that their clean rooms not only meet but exceed industry standards, enabling them to achieve the highest levels of safety and innovation.
Understanding Clean Room Classifications
Clean rooms are meticulously controlled environments where the concentration of airborne particles is regulated to prevent contamination. The level of cleanliness required in a clean room laboratory is determined by the specific needs of the work being conducted, whether it’s in pharmaceuticals, biotechnology, electronics, or any other industry where purity is critical.
To standardize these environments, clean rooms are classified according to the International Organization for Standardization (ISO) standards, which define the maximum allowable particle count per cubic meter of air.
1. Explanation of ISO Standards
ISO clean room classifications range from ISO 1 to ISO 9, with ISO 1 being the cleanest environment and ISO 9 being the least strict.
The classification is determined by the number and size of particles per cubic meter of air. For example, an ISO 1 clean room permits only 10 particles per cubic meter that are 0.1 micrometers or larger, whereas an ISO 9 clean room allows up to 35,200,000 particles of 0.5 micrometers or larger.
These standards help designers and operators create environments tailored to the specific needs of their labs. For instance, a semiconductor lab might require an ISO 3 clean room, where the air is filtered to remove even the tiniest particles that could interfere with microchip production.
On the other hand, a pharmaceutical lab might operate within an ISO 7 clean room, where the focus is on preventing contamination that could affect the sterility of products.
2. Importance of Proper Classification
Selecting the appropriate clean room classification is not merely a regulatory requirement; it is a crucial step in ensuring that the laboratory can effectively support the work it was designed for.
The classification impacts everything from the choice of filtration systems and airflow design to the types of materials used in the construction of the clean room laboratory. An under-classified clean room may lead to product failures, costly recalls, or compromised research, while an over-classified room might result in unnecessary expenses and operational complexity.
Therefore, understanding and correctly implementing ISO classifications is fundamental to creating a clean room that meets the specific demands of a lab’s operations. By aligning the clean room laboratory’s classification with the nature of the work being conducted, clean rooms can optimize their environments to ensure both safety and efficiency, ultimately driving innovation and success in their respective fields.
Essential Design Features of a Clean Room Laboratory
Designing a clean room that consistently maintains its classification and provides a contaminant-free environment requires a comprehensive understanding of the critical features that prevent contamination. These features, from advanced filtration systems to material selection, are the backbone of any successful clean room.
The following key design elements are essential for creating and sustaining a clean room laboratory that meets the rigorous standards of industries like pharmaceuticals, biotechnology, and microelectronics.
1. Airflow and Filtration Systems
One of the most crucial aspects of clean room laboratory design is the control of airborne particles through sophisticated airflow and filtration systems.
High-Efficiency Particulate Air (HEPA) filters and Ultra-Low Penetration Air (ULPA) filters are standard in clean rooms, designed to remove 99.97% and 99.999% of particles, respectively, that are 0.3 micrometers or larger. These filters are typically integrated into the ventilation system to continuously purify the air, ensuring that any particles generated within the room are swiftly removed.
Airflow patterns play an equally important role in maintaining cleanliness. Laminar airflow systems, which direct air in a smooth, unidirectional flow, help to minimize turbulence and reduce the risk of particles settling on surfaces.
In addition, air showers and airlocks are often installed at entry points to remove contaminants from personnel and materials before they enter the clean room, further safeguarding the environment.
2. Material Selection
The choice of materials used in the construction and furnishing of a clean room laboratory is another critical factor in preventing contamination. Walls, floors, and ceilings must be constructed from non-porous, smooth, and easily cleanable materials to prevent the accumulation of particles and facilitate regular cleaning.
Common materials include epoxy-coated surfaces, vinyl flooring, and specialized wall panels designed for clean room applications.
Furniture and equipment within the clean room must also be carefully selected. Stainless steel and powder-coated metals are preferred for their durability and resistance to corrosion and contamination. These materials can withstand the frequent cleaning and disinfecting required in a clean room laboratory environment without degrading or releasing particles into the air.
3. Controlled Entry Systems
Controlling access to the clean room is essential to maintaining its contaminant-free status. To prevent the introduction of external contaminants, dressing areas are usually located at the entrance to the clean room. These areas are designed with strict protocols to ensure that gowns, gloves, masks, and other protective gear are worn correctly.
Pass-throughs and airlocks serve as additional barriers, allowing materials and equipment to enter the clean room laboratory without compromising its cleanliness. Automated systems can further enhance contamination control by regulating access based on clean room classifications, ensuring that only authorized personnel and materials enter the space.
By integrating these essential design features into a clean room, laboratories can create an environment that meets stringent cleanliness standards and supports the advanced work conducted within. Each element, from airflow systems to material choices and access controls, plays a vital role in safeguarding the integrity of the clean room laboratory and the success of the research or production it supports.
Additional Reading: Clinical Laboratory Construction: Building for the Future of Medicine
Critical Clean Room Laboratory Equipment and Tools
Maintaining a contaminant-free environment in a clean room laboratory goes beyond just design—it requires the use of specialized equipment and tools that work together to uphold the stringent cleanliness standards necessary for high-precision work.
From advanced laboratory equipment to environmental monitoring systems and cleaning tools, each component plays a vital role in ensuring that the clean room operates at peak efficiency and maintains its classification.
1. Specialized Laboratory Equipment
In a clean room laboratory, every piece of equipment must be selected and configured to minimize the risk of contamination.
Clean benches, for example, provide a controlled environment where samples can be handled with minimal exposure to airborne particles. These benches use HEPA or ULPA filters to maintain a laminar flow of clean air over the work surface, protecting sensitive processes from contamination.
Fume hoods and containment systems are also critical in clean rooms where hazardous chemicals are used. These devices are designed to capture and contain airborne contaminants at their source, preventing them from spreading throughout the clean room. Their integration into the clean room’s ventilation system is essential for maintaining a controlled environment.
Additional Reading: Decoding Laboratory Fume Hood Design: Best Practices for Safety
2. Monitoring and Control Systems
Real-time environmental monitoring is a cornerstone of clean room laboratory operation. Particle counters, air pressure sensors, and temperature/humidity controls are indispensable tools for tracking the conditions within the clean room. These monitoring systems provide continuous data on key parameters, enabling quick detection and correction of any deviations from the required standards.
Advanced control systems can automate many aspects of clean room management, from regulating airflow and filtration to adjusting temperature and humidity levels. Integration of these systems with alarm and data logging capabilities ensures that any potential issues are promptly identified and addressed, minimizing the risk of contamination.
3. Cleaning and Maintenance Tools
Routine cleaning and maintenance are critical to sustaining the cleanliness of a clean room laboratory. The tools used for these tasks must be specifically designed for clean room environments. Clean room-grade mops, wipes, and disinfectants are essential for removing particles and contaminants from surfaces without introducing new ones.
Regular maintenance protocols, including scheduled filter replacements and equipment calibration, are necessary to ensure that all systems continue to function at their highest level.
By equipping a clean room with the right tools and systems, laboratories can effectively control and monitor their environments, ensuring that their operations remain free from contamination. These critical pieces of equipment and tools not only support the clean room’s function but also safeguard the quality and reliability of the work conducted within, making them indispensable to any successful clean room laboratory.
Additional Reading: The Comprehensive Guide to Laboratory Construction
Best Practices for Maintaining a Contaminant-Free Environment
Even with a meticulously designed clean room laboratory and advanced equipment in place, maintaining a contaminant-free environment requires strict adherence to best practices.
These practices, which cover everything from proper gowning procedures to regular cleaning schedules, are essential for preventing contamination and ensuring the clean room laboratory operates at the highest standards. By following these guidelines, laboratories can minimize risks and maintain the integrity of their clean rooms.
1. Proper Gowning Procedures
The first line of defense against contamination in a clean room laboratory is the proper gowning of personnel.
Every individual entering the clean room must follow a step-by-step gowning procedure designed to minimize the introduction of particles from clothing, skin, and hair. This typically involves donning a full-body suit, gloves, face mask, hair cover, and shoe covers in a designated gowning area.
Training is critical to ensure that all personnel understand and adhere to these gowning procedures. Even a small mistake, such as improperly securing a face mask, can compromise the clean room laboratory environment. Regular refresher courses and monitoring of gowning practices help reinforce the importance of these protocols and ensure that they are consistently followed.
2. Regular Cleaning Schedules
Routine cleaning is essential to maintaining the cleanliness of a clean room laboratory.
A structured cleaning schedule that outlines daily, weekly, and monthly tasks helps ensure that all areas of the clean room are properly maintained.
Daily cleaning of a clean room laboratory typically focuses on critical areas that are more prone to contamination like high-touch surfaces, floors, and workstations, while weekly tasks might include cleaning walls, ceilings, and equipment exteriors. Monthly deep cleans address less accessible areas and involve more thorough procedures.
The use of clean room-compatible cleaning tools and disinfectants is crucial during these routines. These products are specially formulated to remove contaminants without leaving residues or introducing new particles into the environment. Additionally, all cleaning activities should be carefully documented to track compliance and identify any areas needing improvement.
3. Contaminant Control Protocols
Contaminant control in a clean room laboratory goes beyond just cleaning—it also involves strict protocols for handling materials, equipment, and waste.
For example, all materials entering the clean room should be pre-cleaned and, when possible, packaged in a way that minimizes contamination risk. Workflow management is also critical; items should move through the clean room in a manner that reduces cross-contamination, with separate zones designated for different stages of work.
In addition to material handling, proper waste disposal is essential. Waste should be removed from the clean room laboratory in sealed containers to prevent the spread of contaminants. Regular audits of these protocols can help identify potential weaknesses and ensure that all procedures are being followed correctly.
By implementing and consistently following these best practices, laboratories can significantly reduce the risk of contamination in their clean rooms. Proper gowning, regular cleaning schedules, and strict contaminant control protocols are essential to maintaining a controlled environment where high-precision work can thrive. These practices protect the quality of the work being done and contribute to the long-term success and reliability of the clean room laboratory.
Challenges and Solutions in Clean Room Laboratory Maintenance
Maintaining a clean room’s integrity is a continuous process that presents several challenges, from human error to equipment malfunctions and external pollutants.
These challenges can compromise the cleanliness of the environment, potentially leading to costly downtime or compromised results. However, by understanding these challenges and implementing effective solutions, laboratories can overcome obstacles and ensure their clean rooms remain contaminant-free.
1. Common Contamination Sources
One of the most significant challenges in clean room laboratory maintenance is the potential for human error. Despite thorough training and strict protocols, personnel can inadvertently introduce contaminants into the environment through improper gowning, handling materials without proper precautions, or even failing to follow entry and exit procedures correctly.
Equipment malfunction is another common source of contamination. HEPA and ULPA filters, ventilation systems, and monitoring devices are all critical to maintaining a clean room laboratory’s air quality. However, if these systems fail or are not regularly maintained, they can allow particles to accumulate, compromising the clean room’s classification.
External pollutants, such as dust, microbes, and chemicals, pose additional challenges. Even with stringent controls, external contaminants can enter the clean room through gaps in the structure, improperly sealed doors, or materials and equipment brought into the space.
2. Solutions
To address these challenges, laboratories must implement a multi-faceted approach that combines prevention, monitoring, and response strategies.
- Continuous Training and Process Improvements: Regular training sessions and refresher courses for all personnel are essential to minimize human error. These sessions should focus on proper gowning procedures, material handling protocols, and the importance of adhering to clean room standards. Additionally, continuous process improvements, such as refining workflow patterns and enhancing gowning procedures, can further reduce the risk of contamination.
- Regular Equipment Maintenance and Calibration: Preventative maintenance is crucial to avoid equipment malfunctions that could compromise the clean room laboratory environment. This includes scheduled filter replacements, calibration of monitoring devices, and regular inspections of ventilation systems. Keeping detailed records of maintenance activities helps ensure that all equipment functions at peak performance and any potential issues are addressed promptly.
- Implementation of Advanced Monitoring Technologies: Real-time environmental monitoring systems are essential for detecting clean room standard deviations. By utilizing advanced sensors and data logging systems, laboratories can monitor particle counts, air pressure, temperature, and humidity levels continuously. Integrated systems, with automated alerts that notify staff immediately if any parameter falls outside the acceptable range, allow for swift corrective action.
- Enhanced Containment Measures: To prevent the introduction of external pollutants, clean rooms should be regularly inspected for structural integrity, including checking for gaps around doors, windows, and other entry points. Airlocks, pass-through chambers, and other containment measures should be maintained to ensure correct functioning. Additionally, thoroughly cleaning and decontamination is essential before bringing anything into the clean room laboratory.
By proactively addressing these challenges through continuous training, diligent maintenance, advanced monitoring, and stringent containment measures, laboratories can effectively maintain the integrity of their clean rooms. These solutions not only protect the clean room environment but also contribute to the overall success and reliability of the laboratory’s operations, ensuring that the highest standards of cleanliness are consistently met.
Case Studies: Successful Clean Room Lab Designs
Examining real-world examples of successful clean room laboratory designs provides valuable insights into best practices and innovative solutions that can be applied across various industries. These case studies highlight how different sectors have overcome challenges and implemented cutting-edge designs to achieve and maintain contaminant-free environments.
Case Study 1: Pharmaceutical Manufacturing Facility
In the pharmaceutical industry, maintaining a contaminant-free environment is critical to ensuring the safety and efficacy of products. A leading pharmaceutical company sought to upgrade its clean room facilities to meet the increasing demand for biologics, requiring an ultra-clean environment. Designing a clean room that could accommodate high-volume production while adhering to stringent ISO 5 classification standards was the challenge.
- Solution: The design team implemented a modular clean room system with advanced HEPA filtration and laminar airflow to ensure a constant flow of clean air across critical areas. It allowed for flexible expansion and reconfiguration as production needs evolved. Additionally, the facility integrated an automated environmental monitoring system that provided real-time data on particle counts, air pressure, and humidity, ensuring immediate response to any deviations.
- Outcome: The upgraded clean room laboratory successfully maintained ISO 5 classification, even with increased production volumes. The modular design proved highly efficient, allowing the company to quickly scale its operations to meet market demand. The real-time monitoring system enhanced the facility’s ability to maintain consistent environmental conditions, reducing the risk of contamination and ensuring product quality.
Case Study 2: Semiconductor Manufacturing Clean Room
Semiconductor manufacturing requires an extremely clean environment to prevent microscopic particles from interfering with the production of microchips. A leading semiconductor manufacturer faced the challenge of maintaining ISO 3 classification in a high-traffic clean room where precision and contamination control were paramount.
- Solution: The design incorporated a vertical laminar airflow system that directed air from the ceiling to the floor, minimizing particle disturbance and ensuring a downward flow that pushed contaminants away from sensitive equipment. To further enhance cleanliness, the clean room laboratory was outfitted with an advanced gowning system, including automated air showers at entry points to remove any particles from personnel. The facility also utilized a centralized monitoring system to track particle levels, airflow, and temperature continuously.
- Outcome: The semiconductor manufacturer successfully maintained ISO 3 classification, even with the high traffic and complex operations. The vertical laminar airflow system proved effective in minimizing particle contamination, while the advanced gowning and air shower systems significantly reduced the introduction of external contaminants. The centralized monitoring system provided the facility with the data needed to maintain consistent environmental conditions, ensuring the production of high-quality microchips.
Case Study 3: Biotechnology Research Laboratory
A biotechnology research facility specializing in gene therapy required a clean room laboratory environment that met ISO 7 standards and allowed for flexible reconfiguration to accommodate various research projects. The challenge was to design a clean room that supported diverse research activities while maintaining strict contamination control.
- Solution: The clean room was designed with a combination of fixed and mobile partitions, allowing researchers to reconfigure the space as needed for different projects. The facility utilized a multi-stage air filtration system, including pre-filters and HEPA filters, to maintain air quality. Additionally, the laboratory implemented a rigorous training program for all personnel, emphasizing the importance of proper gowning and material handling procedures.
- Outcome: The biotechnology laboratory successfully maintained ISO 7 standards while accommodating a wide range of research activities. The flexible design allowed for easy reconfiguration of the space, enabling the lab to adapt to new projects without compromising cleanliness. The comprehensive training program ensured that all personnel adhered to best practices, minimizing the risk of contamination and supporting successful research outcomes.
These case studies demonstrate the importance of tailored clean room laboratory designs that address the specific needs of different industries. Whether it’s pharmaceutical manufacturing, semiconductor production, or biotechnology research, the key to success lies in combining advanced technologies, flexible design solutions, and rigorous protocols to maintain a contaminant-free environment.
By learning from these examples, laboratories can implement proven strategies to achieve and sustain the highest standards of cleanliness in their facilities.
Additional Reading: Safety and Compliance
Conclusion
Maintaining a contaminant-free environment in a clean room laboratory is a complex and ongoing process that requires careful planning, rigorous implementation of best practices, and the use of advanced technologies. From understanding clean room classifications to integrating essential design features, critical equipment, and stringent maintenance protocols, every detail contributes to the overall success and integrity of the clean room.
However, achieving and sustaining such a high standard of cleanliness can be challenging without the right expertise.
Partnering with a professional laboratory design company that is an accredited member of SEFA (Scientific Equipment and Furniture Association) and OSHA (Occupational Safety and Health Administration) ensures that your clean room is designed and maintained to the highest industry standards. These organizations provide rigorous guidelines and certifications, guaranteeing that your clean room not only meets but exceeds regulatory requirements.
By working with a certified design company like Genie Scientific, you can be confident that every aspect of your clean room laboratory—from initial design to ongoing maintenance—will be handled with the utmost care and precision. This partnership is crucial for ensuring that your laboratory continues to operate efficiently and remains contaminant-free, safeguarding the integrity of your work and the safety of your personnel.