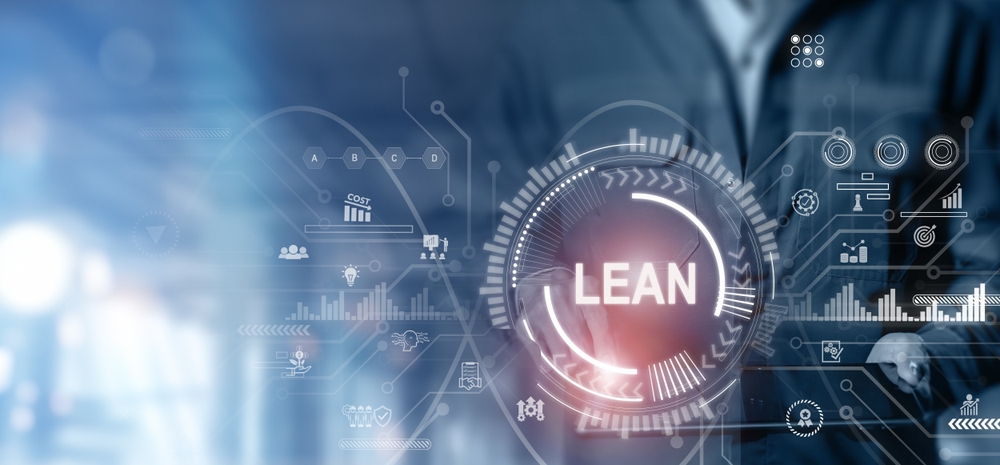
In the fast-paced world of scientific research and clinical diagnostics, efficiency is paramount. Laboratories must not only meet rigorous standards of accuracy but also operate with streamlined workflows to minimize delays and reduce costs. This is where lean design principles come into play, offering a structured approach to optimizing laboratory spaces and furniture layouts.
Originally developed for manufacturing, lean principles focus on eliminating waste, maximizing value, and improving operational efficiency. When applied to laboratory environments, these principles can transform how space, equipment, and furniture are utilized, enhancing productivity and overall performance.
Recent studies underscore the impact of lean methodology in clinical labs, where streamlined layouts and processes have led to measurable improvements. For example, a systematic review of lean applications in clinical settings revealed significant reductions in laboratory turnaround times, demonstrating how such principles can directly benefit workflow efficiency.
This article explores how lean design principles can revolutionize laboratory furniture layouts, from reducing inefficiencies to creating adaptable, ergonomic workspaces tailored to your lab’s unique needs.
What Are Lean Design Principles?
Lean design principles originated in the manufacturing sector, specifically from Toyota’s Production System, where the goal was to maximize efficiency by reducing waste while maintaining high-quality outputs. Over time, these principles have been adapted to various industries, including healthcare and laboratory environments, proving their versatility and effectiveness.
At its core, lean design aims to eliminate any activity or resource that does not add value to the end user. In a laboratory context, this could include unnecessary movement between workstations, excessive inventory of supplies, or inefficient placement of equipment. By streamlining these elements, labs can achieve smoother workflows, faster turnaround times, and a more productive environment.
Lean principles often utilize methods like the 5S framework to improve organization and efficiency in the workplace.
The 5S steps include sorting to remove unnecessary items, setting tools and equipment in order for easy access, shining to keep the area clean, standardizing processes for uniformity, and sustaining efforts to review and improve these practices continuously. This approach helps create a more effective and productive work environment.
Research supports the effectiveness of lean principles in laboratory settings. For instance, a systematic review highlighted how applying lean methodologies in clinical labs resulted in reduced turnaround times and improved operational outcomes. This demonstrates the tangible benefits of adopting lean strategies, particularly when designing lab layouts that prioritize efficiency and value.
By incorporating lean design principles into your laboratory furniture layout, you enhance productivity and create a foundation for continuous improvement, ensuring your lab remains agile and effective in meeting its goals.
Identifying Sources of Waste in Laboratory Layouts
Waste in laboratory environments often goes unnoticed but can significantly impact productivity, safety, and costs. Lean design principles aim to address and eliminate these inefficiencies, starting with identifying the primary sources of waste in a lab setting.
1. Excess Movement
One of the most common inefficiencies in labs is unnecessary movement—whether it’s walking across the room to retrieve equipment, reaching awkwardly for supplies, or relocating samples multiple times during testing. Poorly designed layouts that lack logical workflow paths can lead to wasted time and physical strain on staff.
2. Inefficient Use of Space
Cluttered workstations, misplaced tools, and poorly utilized storage areas contribute to disorganization. Excessive inventory or inadequate storage solutions frequently result in delays, as technicians spend time searching for needed items.
3. Waiting Times
Delays in processing samples or accessing equipment are another significant source of waste. These bottlenecks can occur due to poor layout planning, insufficient resources, or disorganized workflows, directly affecting turnaround times and productivity.
4. Defects and Rework
Errors in experiments or processes often arise from environmental factors like inadequate lighting, uncomfortable furniture, or improperly placed equipment. These conditions not only hinder efficiency but can also compromise accuracy and safety.
5. Underutilized Equipment or Furniture
Labs often invest in specialized furniture and equipment that remains underutilized due to lack of planning or adaptability. Fixed furniture that cannot be reconfigured as needs evolve may result in wasted space and resources.
Real-World Impact of Waste
The cumulative effect of these inefficiencies is substantial. For example, a clinical laboratory implementing lean principles discovered that reconfiguring workstations and reducing unnecessary movement led to faster sample processing and increased staff satisfaction.
By identifying and addressing these sources of waste, laboratories can take the first step toward creating a more efficient and productive workspace. The key lies in strategic furniture placement, modular designs, and thoughtful workflow planning, all of which align with lean design principles.
Designing for Optimal Workflow
A well-designed laboratory layout is fundamental to achieving optimal workflow. By strategically organizing furniture and equipment to support specific processes, labs can reduce inefficiencies and create a seamless environment for productivity and innovation. Lean design principles provide a framework for aligning layout decisions with operational needs.
1. Start with Workflow Mapping
The foundation of an efficient lab layout is understanding how work flows through the space. This involves:
- Identifying key tasks and processes.
- Mapping the movement of materials, samples, and personnel.
- Pinpointing bottlenecks and inefficiencies.
For example, a lab focusing on sample analysis might benefit from organizing zones for sample reception, preparation, testing, and storage in a logical sequence to minimize movement and handling.
2. Establish Task-Specific Zones
Creating dedicated zones for specific activities ensures that tools, equipment, and supplies are readily available where they are needed. Common zones in labs include:
- Research and Analysis: Equipped with specialized furniture like height-adjustable benches.
- Storage: Modular shelving for consumables and equipment.
- Preparation: Compact workstations with easy access to necessary tools.
This zoning approach helps maintain order and prevents cross-contamination or overlap between processes.
3. Prioritize Accessibility and Flexibility
Accessibility to frequently used items is critical for efficiency. Modular and mobile furniture systems are particularly effective in laboratories with evolving requirements. Adjustable benches, rolling carts, and customizable storage units allow for quick reconfigurations to adapt to changing workflows.
4. Ergonomics in Workflow Design
Ergonomics play a significant role in ensuring sustained productivity. Poorly positioned furniture and equipment can lead to fatigue, errors, and even injuries. Incorporating adjustable chairs, workbenches, and proper lighting enhances comfort and aligns with lean principles by reducing waste related to fatigue and errors.
Case Study: Streamlined Layout for Efficiency
A lab specializing in genetic testing reorganized its furniture to follow a lean-inspired workflow. By placing equipment and workstations in proximity to minimize movement, the lab reduced sample processing times by 20%. This approach also improved staff satisfaction by eliminating unnecessary strain and enhancing efficiency.
The Bottom Line
Designing for optimal workflow is about creating an environment where every element serves a purpose. Through careful mapping, task-specific zones, and adaptable furniture, laboratories can achieve layouts that align with lean design principles, reducing waste and enhancing overall performance.
The Role of Lab Furniture in Lean Design
Lab furniture is more than just a functional necessity—it plays a pivotal role in supporting lean design principles. The right furniture can transform a lab’s efficiency, ergonomics, and adaptability, aligning with the core goal of lean design: eliminating waste while maximizing value.
1. Modular Furniture for Adaptability
One of the defining features of lean design is adaptability, and modular furniture systems are the perfect solution. These customizable units allow laboratories to:
- Reconfigure layouts as workflows change.
- Expand or downsize workstations to meet project demands.
- Maximize space utilization without permanent fixtures.
Genie Scientific’s powder-coated modular units exemplify this approach, offering durable, flexible solutions that can be tailored to fit specific lab requirements.
Additional Reading: The Benefits of Mobile Lab Stations: Flexibility and Efficiency
2. Ergonomics for Efficiency
Ergonomically designed furniture contributes directly to lean goals by minimizing physical strain and reducing errors. Features such as adjustable-height workbenches, supportive chairs, and appropriately positioned storage promote:
- Improved comfort for lab staff during long hours.
- Enhanced accuracy and productivity by reducing fatigue.
- Fewer workplace injuries, which can disrupt workflows and increase costs.
3. Storage Solutions to Reduce Clutter
Clutter is a significant source of inefficiency in labs. Well-designed storage furniture helps maintain an organized workspace by:
- Providing easy access to frequently used tools and materials.
- Encouraging adherence to 5S principles like “Sort” and “Set in Order.”
- Reducing time wasted searching for misplaced items.
Vertical shelving, mobile storage units, and compartmentalized drawers can keep workspaces neat and efficient.
4. Durable Materials for Longevity
Lean design also considers long-term value, and the materials used in lab furniture contribute significantly. Powder-coated steel, stainless steel, and other durable materials ensure that furniture withstands rigorous lab environments while minimizing maintenance and replacement costs.
5. Supporting Workflow and Collaboration
Furniture layout influences how team members interact and collaborate. By incorporating lean principles into furniture design, labs can:
- Arrange seating and workstations to support teamwork.
- Create shared spaces for tasks that require group input.
- Enhance communication flow, reducing delays caused by poor spatial organization.
Real-World Benefits
Studies have shown that investing in flexible, ergonomic furniture reduces waste in both time and effort. For instance, a clinical laboratory implementing lean-aligned furniture found that staff could complete tasks more quickly and with fewer errors, directly improving overall productivity.
Lab furniture is a cornerstone of lean design, offering solutions that improve efficiency, adaptability, and comfort. With the right choices, labs can create an environment that not only supports current workflows, but is also ready to adapt to future challenges. Genie Scientific’s range of innovative furniture solutions ensures that every lab can achieve its lean design goals.
Tools and Techniques to Support Lean Layouts
Achieving a lean laboratory layout requires strategic planning and the right tools. By leveraging proven techniques and technologies, labs can optimize their workflows, reduce waste, and foster continuous improvement.
1. 5S Methodology
The 5S framework is a cornerstone of lean design, emphasizing organization and efficiency:
- Sort: Remove unnecessary items from the workspace.
- Set in Order: Arrange tools and equipment for intuitive use.
- Shine: Keep the lab clean and orderly.
- Standardize: Create consistent processes for all tasks.
- Sustain: Regularly review and refine practices.
Applying 5S principles helps create a workspace that supports seamless operations, making it easier to maintain lean layouts over time.
2. Workflow Analysis Tools
Digital tools can provide invaluable insights during the planning phase of a lab layout. Examples include:
- Process Mapping Software: Visualizes workflows to identify bottlenecks and inefficiencies.
- Simulation Tools: Models different layout configurations to determine the most effective design.
- Lab Management Systems: Tracks inventory, schedules, and tasks to streamline operations.
3. Modular Furniture Systems
Modular furniture aligns perfectly with lean principles by offering flexibility and scalability. Features like adjustable-height benches, mobile storage units, and reconfigurable shelving systems allow labs to adapt quickly to changing needs without extensive downtime or costs.
4. Collaborative Planning Techniques
Engaging the team in layout planning ensures that the final design meets practical needs. Techniques include:
- Kaizen Workshops: Collaborative sessions focused on continuous improvement.
- Gemba Walks: Observing workflows directly in the lab to identify waste.
- Feedback Loops: Regularly gathering input from staff to refine layouts and practices.
5. External Expertise
Partnering with experts like Genie Scientific can significantly enhance the layout design process. Their experience in building adaptable and ergonomic furniture ensures that lean principles are embedded into every aspect of the lab’s setup.
Real-World Application of Lean Tools
A clinical laboratory implementing 5S principles and modular furniture systems achieved a 30% improvement in workflow efficiency, as staff no longer had to navigate cluttered workspaces or waste time searching for supplies. This demonstrates the power of combining lean tools with strategic furniture design.
By using the right tools and techniques, laboratories can create a foundation for lean layouts that boost efficiency and productivity. From 5S methodology to advanced workflow analysis tools, every step taken toward lean design ensures a more effective and adaptable workspace.
Benefits of Lean Lab Furniture Layouts
Implementing lean principles in laboratory furniture layouts offers numerous advantages, transforming the way a lab operates and significantly impacting productivity, cost-efficiency, and staff well-being. By focusing on reducing waste and optimizing workflows, labs can create an environment that functions better and adapts to future needs.
1. Improved Efficiency and Productivity
A lean layout reduces unnecessary movement, minimizes downtime, and ensures that staff has easy access to tools, materials, and equipment. With optimized workflows and better organization, lab personnel can complete tasks more quickly, which translates to increased productivity.
For example, studies have shown that by reorganizing lab furniture to reduce physical strain and streamline workflows, staff can focus on their core tasks with fewer disruptions, ultimately accelerating processes like sample analysis and testing.
2. Cost Reduction
A lean layout saves time and reduces costs. By improving space utilization and minimizing waste, labs can make the most of their existing resources. The use of modular, durable furniture, such as Genie Scientific’s powder-coated units, also contributes to long-term savings by reducing the need for costly renovations and frequent replacements.
Furthermore, less time spent searching for equipment or reworking mistakes means fewer labor costs and less wear and tear on resources, all of which contribute to the bottom line.
3. Enhanced Safety and Ergonomics
A cluttered, poorly organized lab can increase the risk of accidents and injury. Lean lab layouts prioritize ergonomics and safety by positioning furniture, equipment, and supplies in a way that reduces the risk of strain, fatigue, and mishaps. Adjustable workstations, proper lighting, and ergonomic seating allow staff to work comfortably, reducing the chance of musculoskeletal disorders and improving overall well-being.
This focus on safety and comfort contributes to a healthier workplace, which benefits staff and helps maintain high levels of productivity.
4. Flexibility and Scalability
As labs evolve, so do their needs. Lean design’s emphasis on flexibility allows lab layouts to easily adapt to new technologies, workflows, or projects. Modular furniture systems, for instance, enable labs to quickly adjust their space as workflows change or new research priorities emerge. This scalability ensures that labs can meet future demands without the need for costly, disruptive renovations.
5. Improved Collaboration and Communication
A well-designed lean layout can foster better collaboration and communication among team members. By organizing spaces for shared tasks, placing equipment within easy reach, and ensuring that staff has clear pathways to each other, lean layouts promote teamwork. This is especially important in labs where multiple people may be working together on complex projects.
Efficiently arranged workstations and collaborative spaces enable quick access to information, equipment, and colleagues, leading to smoother interactions and faster decision-making.
6. Continuous Improvement and Innovation
A lean layout fosters a culture of continuous improvement. With the tools and processes in place to monitor and assess performance, labs can identify areas for further optimization. Feedback loops, regular reviews, and staff involvement in the design process ensure that the lab’s layout evolves alongside advances in technology and methodology.
For instance, ongoing refinements to workflow and layout design can support innovations in research by ensuring that the lab environment remains adaptable and efficient as new processes are introduced.
The benefits of a lean lab furniture layout are far-reaching, impacting everything from day-to-day efficiency to long-term cost savings. By creating an environment that prioritizes organization, ergonomics, and flexibility, labs can boost productivity, improve safety, and create a space that supports continuous improvement and innovation.
Adopting lean principles in lab design isn’t just a short-term fix—it’s an investment in the lab’s future success.
Implementing Lean Design in Your Lab
Implementing lean design principles in your laboratory requires careful planning, collaboration, and a commitment to continuous improvement. While the initial setup may involve time and effort, the long-term benefits of a more efficient, adaptable, and cost-effective workspace are well worth the investment. Here’s a step-by-step guide to help you get started with lean design in your lab.
1. Assess Your Current Layout and Workflow
The first step in implementing lean design is to assess your current laboratory setup. Observe the flow of work, identify areas of waste, and consult staff to gather feedback on pain points. Look for:
- Bottlenecks in the workflow.
- Unnecessary movement or waiting times.
- Disorganized storage or workstations.
- Underutilized equipment or furniture.
Mapping out the current workflow can help you visualize the problem areas and prioritize changes.
2. Define Your Goals
Next, establish clear objectives for your lean design. Are you focusing on improving efficiency, reducing costs, enhancing ergonomics, or creating more flexible spaces? Defining your goals helps guide your decisions throughout the redesign process and ensures that you remain focused on your primary objectives.
It’s important to align these goals with the overall needs of your lab, whether that’s meeting regulatory standards, speeding up sample analysis, or fostering collaboration.
3. Involve Your Team
Successful implementation of lean design requires input from those who will be directly affected: your lab staff. Involve them early in the planning process to gather insights on the challenges they face and the changes they believe would enhance their workflow. Tools like Kaizen Workshops and Gemba Walks can be incredibly helpful in engaging the team in continuous improvement and making sure the design is practical and effective.
4. Choose the Right Furniture and Equipment
Selecting the right furniture and equipment is crucial to supporting lean design. Opt for:
- Modular furniture that can be easily reconfigured.
- Ergonomic workstations to reduce strain and improve comfort.
- Adjustable shelving and storage units to optimize space and improve organization.
- Durable materials that will withstand the demands of the lab environment.
Consider partnering with a supplier like Genie Scientific, which specializes in ergonomic and modular lab furniture solutions designed for lean layouts.
5. Implement the 5S Methodology
As you start to reorganize your lab, apply the 5S principles (Sort, Set in Order, Shine, Standardize, Sustain) to ensure that the space remains clean, organized, and efficient. Begin by sorting out unnecessary items, then arrange the equipment logically for ease of access and use. Regular cleaning and maintenance will also help keep the workspace in top condition.
6. Create Zones and Optimize Layout
Designate specific zones for each task or group of related tasks. Ensure that equipment and materials are placed according to their frequency of use, and eliminate unnecessary movement by positioning items logically. Grouping similar equipment together and ensuring easy access to essential tools will help minimize inefficiencies and reduce time spent searching for items.
7. Monitor, Evaluate, and Improve
Lean design is not a one-time fix but a continuous process. Once your new layout is in place, monitor its effectiveness by tracking key performance metrics, such as turnaround time, staff satisfaction, and error rates. Regularly review the layout and ask for feedback from staff to identify further opportunities for improvement.
This iterative process of evaluating and refining the design ensures that the lab layout evolves alongside new developments and emerging needs.
8. Train and Engage Staff
To sustain lean practices, it’s essential that all staff members understand the principles of lean design and are trained in maintaining the new layout. Regular training sessions, clear communication about expectations, and fostering a culture of continuous improvement will keep lean principles at the forefront of your lab’s operations.
Implementing lean design in your lab is an ongoing journey that requires commitment, collaboration, and flexibility. By starting with a thorough assessment, involving your team, choosing the right furniture, and applying lean methodologies like 5S, you can create a laboratory that enhances productivity, reduces waste, and improves safety.
Remember, the key to successful lean design is continuous improvement—what works today may need to evolve tomorrow, but the benefits of an optimized, efficient workspace will always pay off in the long run.
Additional Reading: Eco-Friendly Laboratory Furniture: Sustainable Options for Modern Labs
Conclusion
Incorporating lean design principles into your laboratory layout is an investment that pays off in efficiency, cost reduction, and long-term adaptability. By focusing on eliminating waste, improving workflows, and creating ergonomic spaces, your lab can become a more productive, flexible, and collaborative environment.
Whether you’re designing a new lab or optimizing an existing one, the right furniture, layout, and tools—along with a commitment to continuous improvement—can help you achieve a truly lean workspace.
By applying lean design principles, you streamline operations and create a space where your team can work more effectively and with greater satisfaction. Lean design is not a one-time effort, but an ongoing process that evolves with your lab’s needs and technological advances.
Ready to optimize your lab layout with lean design principles? Reach out to Genie Scientific today to explore our range of modular, ergonomic lab furniture solutions that can help transform your workspace. Let us guide you toward a more efficient, adaptable, and productive laboratory environment. Contact us to learn more about our customizable options or schedule a consultation to get started on your lean design journey.