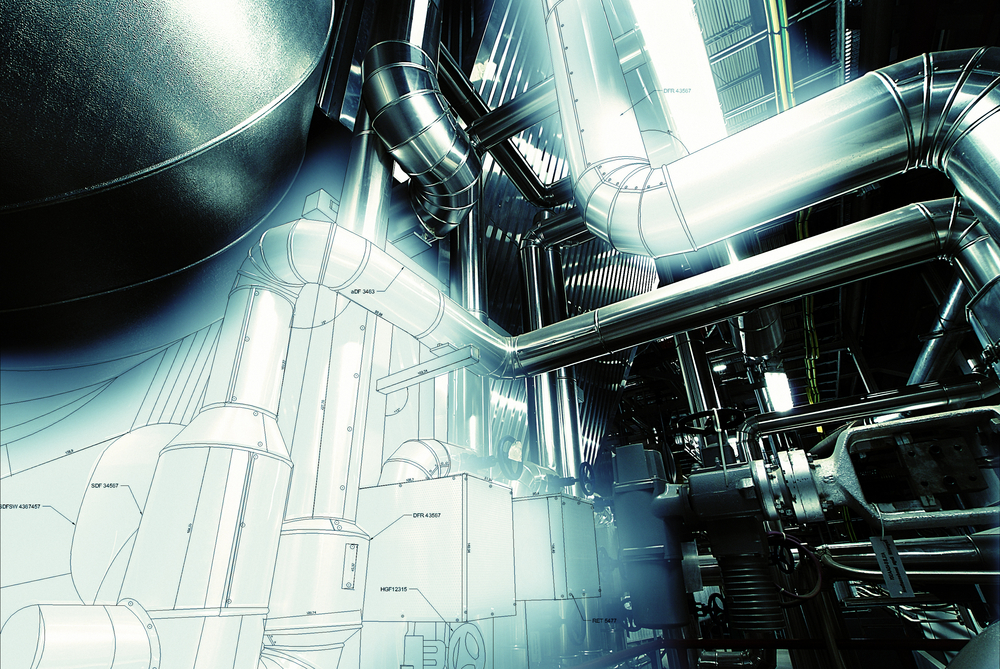
Laboratory construction involves more than just putting up walls and installing equipment. It requires careful planning and execution to create a space that meets the needs of its users while ensuring safety and compliance with regulations.
This comprehensive guide will take you through the essential aspects of laboratory construction, focusing on what comes after the planning and laboratory design stages. We will explore how to integrate equipment and lab furniture seamlessly, catering to the specific requirements of various stakeholders.
From control areas to chemical storage, fume hoods, HVAC systems, plumbing, and gas feeds, we will cover everything you need to know to create a functional and efficient laboratory space. Additionally, we will discuss the importance of power, data, and backup power facilities in ensuring uninterrupted operations.
Whether the laboratory is a new construction from scratch or renovating an existing space, this guide will provide you with the knowledge and insights needed to complete your project successfully.
Obtain a List of Equipment Before Laboratory Construction
For proper laboratory construction planning, obtaining a comprehensive, detailed list of equipment that will be used and installed in the laboratory is crucial. Understanding power, data, and backup power requirements, planning for plumbing and HVAC services, and more plays a crucial role in the lab construction process.
While the type of laboratory construction matters, here’s a comprehensive list of equipment commonly found in laboratories, along with how they might affect power, data, plumbing, and HVAC requirements:
- Fume Hoods: Fume hoods require significant airflow for proper operation, which can impact HVAC requirements. They also need dedicated power outlets.
- Chemical Storage Cabinets: These cabinets need to be properly ventilated and may require specific plumbing for spill containment.
- Laboratory Benches and Tables: These should be sturdy and chemical-resistant. They might require power outlets and data ports.
- Sinks and Eyewash Stations: Sinks require plumbing, and eyewash stations need both plumbing and dedicated power.
- Microscopes and Other Analytical Instruments: These might require stable power supply and data connections.
- Centrifuges and Shakers: These require a stable power supply and may need to be properly grounded.
- Incubators and Ovens: These require a stable power supply and may need ventilation.
- Refrigerators and Freezers: These require a stable power supply and may need backup power sources.
- Autoclaves: These require dedicated power and plumbing.
- Balances and Scales: These require stable surfaces and may need dedicated power outlets.
- Computers and Data Storage Devices: These require stable power supply and data connections.
- Safety Equipment (e.g., Fire Extinguishers, Emergency Showers): These may require specific installation requirements and need to be easily accessible.
- HVAC System: The HVAC system needs to be designed to handle the heat load generated by laboratory equipment and maintain the required temperature and humidity levels.
- Power Backup Systems (e.g., Uninterruptible Power Supply): These may be needed for critical equipment to prevent data loss or damage during power outages.
- Laboratory Furniture: All furniture, including benchtops and work tables, should be designed to accommodate equipment and facilitate easy access to utilities like power and data.
- Monitoring and Control Systems: These systems require data connections and may need dedicated power.
- Waste Management Systems: These require proper plumbing and may need to meet specific safety standards.
By considering these equipment requirements as included in the lab design guide, and collaborating with the architect, lab designer, and mechanical, electrical, and plumbing engineers, you can ensure successful laboratory construction that meets the needs of its users while maintaining safety and compliance with regulations.
Determining Control Areas for Chemical Storage
Control areas within the laboratory facilities are designated spaces where chemicals are stored and handled. These areas require careful consideration in construction planning. They are crucial for ensuring the safety of laboratory personnel and require compliance with regulations such as NFPA45 (National Fire Protection Association), IBC (International Building Code), and IFC (International Fire Code). Furthermore, the CDC partners with the U.S. National Institutes of Health (NIH) to publish biosafety guidelines for protecting workers and preventing exposures in biological laboratories.
While basic chemical safety standards cover all laboratories, specialized labs like those working with radioactive materials or other biosafety risks and hazardous materials must comply with additional regulations. It is wise to involve the Environment, Health and Safety (EH&S) in the schematic phase of laboratory construction planning.
To determine the appropriate size and location of control areas, consider the following factors:
1. Chemical Inventory: Begin by conducting a thorough inventory of all chemicals used in the laboratory. This includes identifying the types and quantities of chemicals present.
2. Chemical Hazard Classification: Classify chemicals based on their hazards (e.g., flammable, corrosive, toxic) to determine the level of control required.
3. Storage Requirements: Refer to the NFPA45, IBC, and IFC standards to determine the specific requirements for storing different types of chemicals. This includes guidelines for storage cabinets, shelving, biosafety cabinets, and segregation of incompatible chemicals.
4. Ventilation: Ensure that control areas are equipped with adequate ventilation systems to prevent the buildup of hazardous fumes or vapors.
5. Access and Egress: Design control areas with clear access and egress routes to facilitate safe and efficient movement of personnel and equipment.
6. Fire Protection: Install appropriate fire protection measures, such as fire extinguishers, sprinkler systems, and fire-rated walls, to minimize the risk of fire spreading beyond the control area.
7. Signage and Labeling: Clearly label control areas with signage indicating the hazards present and any required safety precautions.
8. Emergency Response: Develop and implement an emergency response plan specific to the hazards present in the control area, including procedures for spill containment and evacuation.
By carefully considering these factors and complying with the relevant standards, you can ensure that the laboratory’s control areas are designed to safely and effectively store and handle chemicals.
Heating, Ventilation, and Air Conditioning
In the context of laboratory construction, the ventilation system within the HVAC system specifically focuses on providing a controlled environment for air quality, temperature, and humidity within the laboratory space. This includes considerations such as the design and placement of air vents, ductwork, and exhaust systems to ensure proper airflow and containment of contaminants.
Ventilation is a critical aspect of laboratory construction, as it plays a key role in maintaining a safe and healthy environment for laboratory personnel. Here are some key considerations for ventilation systems in laboratory construction:
1. Fume Hoods
Laboratory fume hoods should be properly designed, located, and maintained to ensure effective containment and removal of hazardous fumes and vapors. The ventilation system should provide an adequate flow of air into the hood and safely exhaust it outside the building.
2. General Laboratory Ventilation
The laboratory should have a general ventilation system that provides a continuous supply of fresh air and removes stale air. This helps maintain a comfortable working environment and reduces the risk of exposure to airborne contaminants.
3. Airflow Patterns
The ventilation system should be designed to create airflow patterns that minimize the spread of contaminants within the laboratory. This may involve the use of directional airflow and containment strategies to prevent cross-contamination between different work areas.
4. Exhaust Systems
Exhaust systems should be designed to safely remove hazardous fumes and vapors from the laboratory. This may involve the use of dedicated exhaust systems for specific equipment or processes, such as fume hoods and chemical storage areas.
5. Air Filtration
The ventilation system should be equipped with appropriate filters to remove particulate matter and other contaminants from the air. HEPA filters are commonly used to achieve high levels of air cleanliness in laboratory settings.
6. Pressure Differentials
The laboratory should be maintained at a slight negative pressure relative to adjacent areas to prevent the escape of contaminants. This helps contain hazardous substances within the laboratory and protects the surrounding environment.
7. Monitoring and Alarm Systems
The ventilation system should be equipped with monitoring sensors to detect any malfunctions or deviations from normal operating conditions. Alarm systems should be in place to alert personnel to potential hazards.
8. Compliance with Standards
The ventilation system should comply with relevant standards and regulations, such as those set forth by the American Society of Heating, Refrigerating and Air-Conditioning Engineers (ASHRAE) and the Occupational Safety and Health Administration (OSHA).
By carefully evaluating these ventilation system considerations in the laboratory construction planning, a safe, and efficient working environment for laboratory personnel can be created.
Ductwork
When considering fume hood ductwork in laboratory construction, several important factors come into play, including:
1. Integration with Existing HVAC System
The fume hood ductwork needs to be integrated into the existing HVAC system of the building. This involves ensuring that the ductwork is properly connected to the ventilation system to safely exhaust fumes outside the building.
2. Location in a Multistory Building
The location of the fume hood and its ductwork in a multistory building is crucial. The ductwork needs to be routed in a way that minimizes the distance and number of bends to maintain proper airflow and efficiency.
3. Routing of Ductwork
The ductwork for the fume hood needs to be carefully routed to ensure that it does not interfere with other building systems or occupant spaces. This may involve running the ductwork vertically through multiple floors to reach a safe outlet for the fume blower.
4. Compliance with Regulations
The design and installation of the fume hood ductwork must comply with relevant regulations and standards, such as those set forth by the NFPA, IBC, and IFC, to ensure the safe handling and exhaust of hazardous fumes.
5. Efficiency and Safety
Proper design and installation of the ductwork are essential for ensuring the efficient and safe operation of the fume hood. This includes using the correct size and material for the ductwork to prevent leaks and maintain proper airflow.
By considering these factors, you can ensure that the fume hood ductwork in your laboratory is properly designed and installed to safely exhaust hazardous fumes outside the building, while also minimizing the impact on the building’s existing HVAC system and occupant spaces.
Plumbing
Plumbing considerations are critical in laboratory construction to ensure the safe and efficient operation of various equipment and processes. Here are some key plumbing considerations for laboratory construction:
1. Sinks
Laboratories require sinks for handwashing and cleaning equipment. These fixtures should be strategically located and connected to the plumbing system to ensure easy access and proper functionality.
2. Chemical Waste Management
Laboratories generate chemical waste that must be properly managed and disposed of. Plumbing systems should include provisions for collecting, storing, and disposing of chemical waste in compliance with regulations.
3. Vacuum Systems
Some laboratory equipment, such as vacuum pumps, require a vacuum system for operation. Plumbing systems should include provisions for connecting and distributing vacuum lines to the required locations.
4. Deionized Water Systems
Laboratories often require deionized water for experiments and processes. Plumbing systems should include provisions for supplying and distributing deionized water to the required locations.
5. Emergency Showers and Eyewash Stations
Laboratories should be equipped with emergency showers and eyewash stations for use in case of chemical exposure. Plumbing systems should include provisions for supplying these fixtures with water at the required flow rates and pressures.
6. Floor Drains
Laboratories should be equipped with floor drains to facilitate the cleaning and drainage of spills and other liquids. Plumbing systems should include provisions for connecting these drains to the building’s wastewater system.
7. Specialized Equipment
Some laboratory equipment, such as autoclaves and sterilizers, may require specialized plumbing connections. Plumbing systems should include provisions for connecting these types of equipment to the required utilities.
By considering these plumbing considerations during the design and construction of a laboratory, you can ensure that the plumbing system meets the specific needs of the facility and complies with relevant regulations and standards.
Gas Lines
Considerations for gas lines in laboratory construction are essential to ensure the safe and efficient operation of gas-powered equipment, such as burners on lab benches and worktables. Here are some key aspects to look at:
1. Gas Type
Determine the type of gas or gases that will be used in the laboratory (e.g., natural gas, propane, hydrogen, etc.). Ensure that the gas lines and equipment are compatible with the gas type.
2. Gas Supply
Ensure that an adequate and reliable gas supply is available for the laboratory. This may involve connecting to a central gas supply system or using gas cylinders.
3. Gas Line Installation
Install gas lines in accordance with local building codes and safety regulations. Use materials that are suitable for the gas type and pressure, such as steel or copper pipes.
4. Gas Pressure Regulation
Install pressure regulators and safety valves to control the gas pressure and ensure safe operation. Pressure should be regulated based on the specific requirements of the equipment being used.
5. Gas Line Sizing
Size gas lines appropriately to ensure an adequate flow of gas to each burner or piece of equipment. Consult a professional to determine the correct pipe diameter and layout.
6. Gas Line Placement
Place gas lines in locations that minimize the risk of damage or interference. Avoid routing gas lines near sources of heat, electrical equipment, or other hazards.
7. Gas Line Labeling
Label gas lines clearly to indicate the type of gas, pressure rating, and any other relevant information. This helps prevent confusion and ensures that the lines are used correctly.
8. Gas Line Maintenance
Regularly inspect and maintain gas lines to ensure they are in good condition and free from leaks. Follow the manufacturer’s recommendations for maintenance and inspection.
By considering these gas line considerations during laboratory construction, you can ensure that the gas supply system is safe, reliable, and meets the needs of the laboratory’s operations.
Power
Power supply and outlets are crucial in laboratory construction to ensure that the facility can safely and efficiently power all equipment and instrumentation. Here are some key considerations:
1. Power Requirements
Determine the power requirements of all equipment and instrumentation in the laboratory, including lighting, HVAC systems, fume hoods, and analytical instruments. Ensure that the electrical system is designed to handle the total power load of the laboratory.
2. Dedicated Circuits
Install dedicated circuits for high-power equipment to prevent overloading and ensure safety. Equipment such as autoclaves, ovens, and large centrifuges may require dedicated circuits.
3. Backup Power
Consider installing backup power systems, such as uninterruptible power supplies (UPS) or generators, to ensure continuous power supply in case of outages. Critical equipment and instrumentation should be connected to these backup power sources.
4. Grounding
Proper grounding is essential to prevent electrical shocks and ensure the safe operation of equipment. Ensure that all electrical outlets and equipment are properly grounded according to electrical codes and standards.
5. Location of Outlets
Install power outlets at convenient locations throughout the laboratory to accommodate the placement of equipment and instrumentation. Consider the layout of benches, tables, and workstations when determining outlet locations.
6. Safety Considerations
Install ground fault circuit interrupters (GFCIs) in areas where water or moisture is present to prevent electrical shocks. Ensure that all electrical work is performed by qualified personnel in compliance with local electrical codes.
7. Future Expansion
Consider future expansion and growth when designing the electrical system. Install additional outlets and circuits to accommodate future equipment and instrumentation needs.
8. Integration with Building Management Systems
Integrate the electrical system with the building management system (BMS) to monitor and control power usage, optimize energy efficiency, and ensure safety.
By considering these power supply and outlet considerations during laboratory construction, you can ensure that the facility has a safe, reliable, and efficient electrical system to meet its operational needs.
Data Connections
Data connection installations are critical in laboratory construction to enable the facility to support the communication and data needs of modern scientific research. Here are some key considerations:
1. Network Infrastructure
Install a robust network infrastructure capable of supporting high-speed data transmission. This includes network cables, switches, routers, and wireless access points.
2. Data Security
Implement data security measures to protect sensitive information. This may include encryption, firewalls, and access controls.
3. Redundancy
Consider implementing redundant network connections to ensure continuous connectivity in case of network failures. This may involve using multiple Internet service providers (ISPs) or redundant network paths.
4. Bandwidth Requirements
Determine the bandwidth requirements of the laboratory, taking into account the data transfer needs of equipment, instrumentation, and users. Ensure that the network can support these requirements.
5. Integration with Laboratory Equipment
Ensure that laboratory equipment and instrumentation can be easily connected to the network for data transfer and remote monitoring. This may involve installing Ethernet ports or wireless connectivity options on equipment.
6. Location of Data Outlets
Install data outlets at convenient locations throughout the laboratory to accommodate the placement of equipment and workstations. Consider the layout of benches, tables, and workstations when determining outlet locations.
7. Future Expansion
Consider future expansion and growth when designing the network infrastructure. Install additional data outlets and network capacity to accommodate future equipment and instrumentation needs.
8. Compliance
Ensure that the network infrastructure complies with relevant standards and regulations, such as those related to data security and network performance.
By considering these data connection considerations during laboratory construction, you can ensure that the facility has a reliable and efficient data infrastructure to support its scientific research activities.
ADA Considerations
When constructing a laboratory, it is essential to consider compliance with the Americans with Disabilities Act (ADA) to ensure that the facility is accessible to individuals with disabilities.
This includes providing accessible routes of travel throughout the laboratory, including entrances, corridors, staircases, and work areas. The lab design team will take care of ensuring accessibility of lab workbenches, casework, chairs, and other lab furniture and equipment in the design process.
Properly designed and located signage, as well as accessible restroom facilities, are also important considerations. By incorporating these ADA requirements into the construction of the laboratory, you can create a space that is inclusive and accessible to all individuals, regardless of their abilities.
Conclusion
Laboratory construction requires careful planning and attention to detail to ensure the safety and efficiency of its operations. From determining control areas for chemical storage to installing ventilation systems and gas lines, every aspect of laboratory construction plays a crucial role in creating a functional and safe working environment.
This comprehensive guide has covered the essential considerations for laboratory construction, including the integration of equipment and lab furniture, compliance with regulations, and the importance of proper ventilation, plumbing, power supply, data connections, and gas lines. By following these guidelines and considering the specific needs of your laboratory, you can create a facility that meets the highest standards of safety and functionality.
Building a laboratory is not just about constructing a physical space; it’s about creating an environment that fosters innovation, collaboration, and scientific discovery. By investing in the proper design and construction of your laboratory, you can create a space that enables researchers to push the boundaries of knowledge and make meaningful contributions to their fields.
We hope that this guide has provided you with the information you need for a successful laboratory construction that meets your needs and exceeds your expectations. If you have any further questions or need assistance with your laboratory construction project, please do not hesitate to contact Genie Scientific, your single-source solution for laboratory design and construction.